This is featured post 2 title
Replace these every slider sentences with your featured post descriptions.Go to Blogger edit html and find these sentences.Now replace these with your own descriptions.
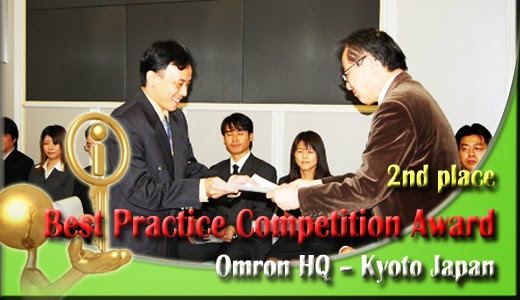
This is featured post 3 title
Replace these every slider sentences with your featured post descriptions.Go to Blogger edit html and find these sentences.Now replace these with your own descriptions.
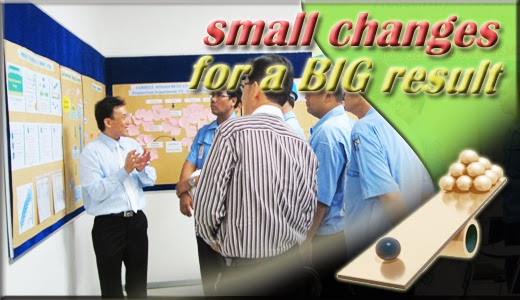
This is featured post 4 title
Replace these every slider sentences with your featured post descriptions.Go to Blogger edit html and find these sentences.Now replace these with your own descriptions.
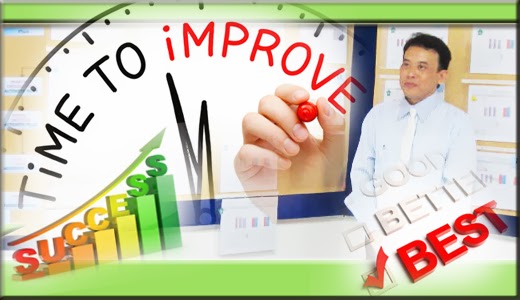
Rabu, 01 Juli 2015
Jebakan Batman sebuah Sistem (IT)
Beberapa waktu yang lalu saya mengunjungi sebuah bengkel resmi dari salah satu ATPM terkenal di tanah air untuk keperluan service rutin penggantian oli dan penggantian filter oli.
Dari halaman depan bengkel tersebut sudah di sambut oleh bapak security yang menyambut dengan hangat dan mempersilahkan untuk masuk dan menunggu di dalam ruang tunggu. Memasuki ruang tunggu saya disambut dengan sebuah monitor touch screen untuk mengambil nomor antrian. Saya memencet salah satu pilihan dan mulai mencari tempat duduk untuk menunggu. Ruangan tunggu sangat nyaman dan membuat betah orang yang menunggu. Mulailah saya menunggu.... 5 menit .... 15 menit... 30 menit ..... 1 jam..... mulailah saya gelisah.... mengapa nomor saya tidak dipanggil-panggil. Sampai 1 jam 20 menit saya sudah tidak sabar dan langsung ke petugas Customer Care yang menyambut dengan hangat. Saya bertanya ke petugas "Mengapa nomor saya tidak di panggil?"...... jawaban inilah yang mentriger saya menulis di Corner ini.
Sang petugas bertanya "Bapak nomor berapa ?" jawab saya nomor XXX.
"Oh bapak menunggu 2 nomor antrian lagi"... sabar ya pak, sahutnya.
Saya menjawab "Apakah tidak ada cara lain untuk mendaftar untuk pekerjaan ganti oli... " saya SUDAH MENUNGGU lebih dari 1 jam cuma untuk keperluan mendaftar jasa ganti oli... belum menunggu antrian ganti oli dan menunggu proses penggantian oli.
Sahut petugasnya "Kita sudah mempunyai sistem antrian yang canggih pak.... sudah computerized.. semua transparant.... bapak bisa melihat progress dari pekerjaan kami di layar monitor besar yang ada di dinding. Tidak ada yang main belakang dulu duluan... semua urut kedatangan. Sistem sudah teruji dengan baik.... dengan tujuan Pelanggan puas. Bapak bisa juga booking lewat telp untuk menghindari antrian yang panjang....
Inilah yang saya katakan sebuah Jebakan Batman.....
Bayangkan, saya menghabiskan waktu 1 jam 20 menit untuk proses registrasi. Setelah itu menunggu lagi hampir 2 jam (menurut informasi petugasnya) baru kendaraan saya di lakukan proses penggantian oli yang membutuhkan waktu tidak lebih dari 30 menit. Sehingga total waktu yang dibutuhkan untuk proses penggantian oli adalah 3 jam 50 menit / 230 menit.
Kalau menggunakan konsep KAIZEN, bisa dihitung Value Added (VA) activitynya di proses penggantian oli (30 menit) sebesar 13%... sedangkan proses menunggu yang menerupakan Non Added Value (NVA) sebesar 83%.
Inikah yang dimaksud dengan sistem yang Canggih dan Computerized .....????
Inilah yang saya maksud sebuah Jebakan Batman....................
Pada awalnya, Jajaran Pucuk Pimpinan (Plant Manager, Direksi dan bahkan CEO) menganggarkan dana yang sangat besar untuk membangun sebuah sistem IT yang sangat canggih dengan harapan akan meningkatkan kinerja persusahaan. Tetapi mereka seringkali lupa untuk melihat bagaimana hasil implementasinya..... bagaimanakah efek dengan kemajuan perusahaan. Mereka seakan tersihir bahwa dengan implementasi IT.... semua masalah bisa teratasi.
Ironisnya... karyawan operasional... jadi sangat sangat tergantung dengan sistem tersebut mereka lupa dengan keadaan di lapangan. Bagian operasional seakan tersihir bahwa mereka telah bekerja dengan sangat baik karena telah dituntun dengan sistem IT yang canggih dan mahal..... Fokus mereka beralih dari Proses di lapangan ke Computer.
Kalau mengambil contoh kasus antri di penggantian oli tadi, mereka sudah lupa dengan FUNGSI DASAR mereka bekerja di perusahaan tersebut untuk apa? mereka lupa dengan INTI pekerjaan mereka yaitu mengganti oli, mereka lebih berkonsentrasi di bagaimana menghandle antrian customer.
Mereka tidak improve di bagian bagaimana mempercepat proses penggantian oli.... tetapi mereka malah berkonsentrasi bagaimana agar customer bisa nyaman dengan cara yang kurang tepat (ada Wifi, Canteen, full AC, music,dsb)
Oleh karena itu di dalam implementasi KAIZEN sangatlah penting untuk tetap melihat keadaan di lapangan dengan konsep 3-GEN yaitu Gemba (Lapangan) - Gembutsu (Actual thing) dan Genshou (Fenomena yang terjadi).
Apalagi di industri manufacture, 3-GEN ini sangatlah penting. Inilah sebenarnya Streng Point yang harus dimiliki oleh perusahaan manufacture. Semakin tinggi skill 3-GEN nya semakin tinggi pula Manufacturing Skill yang dimiliki oleh suatu perusahaan.
Apakah itu berarti penggunaan IT adalah salah ?.... tidak juga tetapi yang perlu dipahami adalah POLA PIKIR pemakaiannya.
Sistem IT adalah salah satu TOOLS BANTU dalam bekerja...... BUKAN INTI DARI PEKERJAAN.
Sistem IT berguna untuk mempercepat proses pengolahan data... dan berujung ke KECEPATAN Pengambilan Keputusan.
Berikut ini adalah beberapa contoh dari pengalaman saya tentang penggunaan Sistem IT yang berefek negatif.
1. Ada seorang Warehouse Supervisor di perusahaan manufacture yang sampai dapat Surat Peringatan (SP) karena nilai inventorynya sangat kecil secara sistem tetapi di lapangan ditemukan banyak Barang di Warehouse dan beliau tidak dapat membuktikan mengapa hal itu sampai terjadi. Alhasil..... bagian keuangan binggung mengunakan data yang mana? Actual Sistem atau Actual Lapangan......
2. Di suatu departemen Warehouse di sebuah perusahaan sampai meminta PO tambahan ke Supplier (tanpa perlu mengirim barang) karena secara sistem barang masih kurang padahal secara actual barang sudah terkirim. Suplier tidak mau membuat PO tambahan.... karena cacat sistem... akhirnya Death Lock
3. Pernah juga ada yang situasinya terbalik .... ini yang sering terjadi.... Di sistem ada barang tetapi actual barang sudah terpakai.......
4. Seorang Direktur baru beberapa bulan menjabat (kebetulan Exspatriat Jepang) mengatakan.... "I don,t know what happen in this company, in the system we have a lot of money but in the bank we don,t have the money".......^$#^#$^$#@
5. Seorang direktur manufacturing company mengatakan...... "Saya tidak pernah percaya dengan data yang di sampaikan oleh manager saya meskipun itu hasil olahan sistem, Data bisa dibuat.... actualnya bulan lalu biaya reject saya sangat sangat tinggi.
Itulah beberapa comment dari pelaku di industri manufacturing tentang penggunaan suatu sistem / pengolahan data.
Saya sangat setuju sekali dengan ucapan salah seorang Plant Manager di perusahaan Automitive Parts company yang telah selesai melakukan Improvement Development Project dengan saya dan telah dapat meningkatkan Produktifitas sampai dengan 40%. Beliau mengatakan..... "Biarlah anak-anak stabil dulu dengan apa yang terjadi di lapangan... baru saya akan mengimplementasikan sistem IT yang lebih tinggi tingkatannya".
Demikianlah ulasan saya tentang implementasi sistem (IT).
Untuk itu kita harus cermat mengimplementasikan sistem (IT)
IT System Implementation MUST Be Match with Actual (Gemba) condition .... this is STRONG POINT of Manufacturing Company....actualy
Cikarang, Awal Juli 2015
Rabu, 08 April 2015
Mengapa Konsep Total Productive Maintenance (TPM) Gagal di Implementasikan.....
Beberapa waktu yang lalu saya berdiskusi dengan salah satu Production Manager di sebuah industri manufacture yang sudah malang melintang di dunia industri lebih dari 15 tahun. Sebut saja dengan Manager Veteran.
Kita berdiskusi tentang implementasi TPM di perusahaan tempat beliau bekerja dan kondisi manufacture di Indonesia saat ini.
Manager Veteran bercerita kalau TPM sudah berjalan lebih dari 7 tahun dan sudah berulang kali melakukan kompetisi di Jepang sebagai Head Office Companynya.
Saya mengatakan... it's Very Great.... kemudian saya bertanya, apa yang dirasakan sekarang di Production Area ? tentunya productivitas akan tinggi dan semuanya terkendali dengan baik karena sudah menjalankan TPM cukup lama. Tetapi jawabannya sangat mengejutkan saya. Manager Veteran bercerita.... Oh sama saja keadaannya seperti sebelum konsep TPM dijalankan. Wah ini menarik, pikir saya.
Sama bagaimana sahut saya? ya sama saja.. masih banyak terjadi masalah mesin Break Down dan Production Planning yang tidak terpenuhi kata Manager Veteran.
Tolong ceritakan ke saya bagaimana cara merecord dan mengimplementasikan perhitungan OEE..? hal ini saya tanyakan karena Point Penting di dalam konsep TPM adalah cara merecord dan menghitung hasil OEE.
Manager Veteran mengatakan... Wah... kita kesulitan merecord dan menghitung hasil OEE karena mesin kita sering berhenti dan juga Order yang masuk dari PPIC sangat fluktuatif sekali. Akhirnya kita sekedar merecord hasil OEE dan beberapa kali kita "tembak".....
Woahhh... kata saya.......
Beliau melanjutkan ceritanya.... akhirnya lama kelamaan Atasan dan kita sendiri tidak percaya dengan hasil OEE dan tidak menggunakannya sebagai parameter pengukuran Produkticitas...
Lantas menggunakan cara apa sekarang...? kata saya?
Kita menggunakan parameter Target Vs Actual sebagai parameter Productivitas.
Oh ... berarti kembali ke konsep Konvensional lagi dong.... sahut saya.
Iya bisa dikatakan demikian.... sahut Manager Veteran.....
Itulah sedikit gambaran tentang kegagalan yang dialami dalam menjalankan konsep TPM.
Kemudian apa penyebabnya? apakah hanya masalah konsistensi Recording saja?
Sepintas memang demikian .... tetapi menurut saya bukan Konsistensi Recording penyebab utamanya. Penyebab Utamanya adalah Kesalahan Konsep Berpikir dari Management Level tentang Konsep Implementasi TPM.
Kebanyakan Orang beranggapan bahwa TPM adalah sekedar Program Maintenance atau Tools untuk merecord Breakdown mesin atau bahkan bahkan untuk catatan History Mesin saja. Padahal TPM adalah sebuah POLA PIKIR tentang bagaimana melakukan Management Control di area Produksi (bahkan Company, karena TPM juga melibatkan departemen terkait seperti PPIC, Purchasing, Quality, dll meskipun memang Core nya di Production Area).
TPM adalah POLA PIKIR memaintain 4M (Man - Material - Method - Machine) di area Produksi...
TPM adalah tempat untuk merubah pola pikir karyawan dari metode Konvensional menjadi metode OEE (Overall Equipment Effectiveness).
TPM adalah sabagai tempat Data Center tentang permasalahan-permasalahan yang terjadi sepanjang proses produksi di jalankan.
Konsep TPM akan membuka kita semua tentang MASIH ADAKAH RUANG IMPROVEMENT di AREA PRODUKSI ? bukan hanya sekedar Recording tentang Productivitas.
Sebagai bahan Review marilah kita lihat bersama tentang Bagan Konsep perhitungan OEE dibawah ini.
Dari bagan OEE diatas terlihat bahwa setiap Losses yang muncul selama proses produksi berlangsung akan ditangkap oleh kotak kotak Losses yang ada dan dibagi menjadi 4 Kotak Losses yaitu:
1. Management Losses, yang akan menangkap Losses yang diakibatkan oleh keputusan Management seperti: Briefing sebelum bekerja, Pemakaian alat APD (Alat Pangaman Diri), kegiatan 5S, dll.
2. Problem Losses, yang akan menangkap Looses yang diakibatkan karena problem yang timbul selama proses produksi berlangsung dan dapat ditangkap dengan mata langsung seperti: Break Down mesin, Setup Mesin, Parts Shortage.
3. Minor Stoppage, yang akan menangkap Losses yang diakibatkan karena problem yang muncul dan tidak dapat ditangkap mata secara langsung seperti, Idle Mesin, Loss Control.
4. Inferior Losses, yang akan menangkap Losses dari Inferior Produk.
Masing-masing Losses tersebut kemudian di convert ke bentuk bilangan yaitu:
1. OTR = On Time Ratio atau dikenal juga dengan Availability Ratio. yang menunjukkan performance kehandalan mesin serta operasionalnya (setup, parts shortage)
2. PER = Performance yang menunjukkan Management Skill Production Member dalam menangkap Losses yang tidak kelihatan mata secara langsung.
3. QR = Quality Ratio yang menunjukkan Ratio Kualitas Produk yang dihasilkan.
4. Total Performance dihitung dengan OEE yang didapat dengan mengalikan OTR, PER dan QR.
Dengan rumusan diatas sangat jelas terlihat bahwa Tujuan Utama dari Konsep perhitungan OEE adalah untuk melihat seberapa Losses yang muncul di dalam proses produksi kita, bukan hanya recording saja.
Dengan mengungkapkan semua Losses yang muncul maka akan dengan mudah kita menangani problem yang ada dan ini artinya menaikkan Angka Produktifitas suatu Proses.
Kemudian, timbul pertanyaan .... Lantas.... Apakah Kelebihan Nyata dari metode perhitungan OEE diatas?
Mari kita lihat bagan Perbandingan dibawah ini yang menggambarkan Perbandingan Perhitungan Produktifitas dengan menggunakan metode yang Konvensional dengan menggunakan metode OEE.
Dapat terlihat bahwa di dalam metode perhitungan Konvensional (kolom sebelah kiri), Losses yang ditangkap hanya Management Losses dan Mesin Rusak sehingga hasil perhitungan Productivitynya mencapai angka 90%.
Apa akibat dari angka 90% tersebut?
Kita semua merasa senang karena Ratio Productivitas kita tinggi yaitu 90%. Dan angka ini pula yang disampaikan ke Atasan kita...... dan Ironisnya atasan kita juga senang dengan angka 90% tersebut..... Inilah salah satu POLA PIKIR yang diterjemahkan SALAH oleh Management Level (Pola pikir Management... tertingginya 100%... jadi kalau sekarang hasilnya 90%... ya baguslah) dan hal tersebut banyak yang tidak menyadarinya.
Hal ini juga yang menjadikan tanya jawab besar...... Mengapa Produktifitasnya tinggi tetapi Delivery Performancenya Rendah dan masih sering mendapat Customer Complain tentang Delivery)......
Pertanyaan ini sering tidak bisa terjawab oleh banyak Management Level sampai sekarang...
Sekarang mari kita masukkan data yang ada dengan menggunakan metode OEE (kolom samping kanan) dimana semua Losses kita hitung..... apa hasilnya ? Angka Productivitas kita menjadi rendah sekali yaitu 71%.
.... Nah disinilah masalah itu muncul ? Beranikah kita menyatakan bahwa angka Produktifitas kita di angka 71%....? Pasti Management Level akan bertanya (dengan nada marah pastinya) mengapa kok rendah sekali...? (Mengapa rendah? karena Pola pikirnya MAX 100%, kalau sekarang 70%.... ya rendah). Daripada kita yang kena marah maka sebaiknya tidak menggunakan formula ini.
Bahkan pernah terjadi Management Level juga tidak senang dengan angka ini... karena.... angka ini akan di pandang rendah oleh Customer jika bertanya tentang angka produktifitas kita.... dan ada kemungkinan Customer tidak jadi order atau stop order........
Pemahaman inilah yang banyak terjadi dan menyebabkan TPM tidak 100% dijalankan dan banyak yang beranggapan bahwa Konsep TPM adalah Jelek....
Rangkaian cerita diatas adalah sebagai jawaban Mengapa TPM sangat sulit sekali di implementasikan di Indonesia (atau bahkan di perusahaan di luar Indonesia).
Padahal dari pengalaman saya, OEE di angka 85% saja... itu adalah Angka Productivitas yang sudah luar biasa BAGUS dan perlu energi Ekstra untuk mencapainya dan Delivery Performance sudah bisa mencapai 99,... %
Mengapa demikian ?
1. OEE tidak mungkin 100%, dengan Management Losses yang ditetapkan 20 menit saja ... OEE Max 96%
2. Di dalam proses produksi pasti terjadi Setup Time ataupun Change Type
3. Manusia ataupun Mesin tidak mungkin berjalan terus tanpa Idle Time.
4. Inferior Produk masih muncul
Untuk itu, untuk menjalankan Konsep TPM, salah satu hal utama yang harus dirubah adalah POLA PIKIR tentang angka Produktifitas.
Masihkah kita Nyaman dengan angka 90%, yang kelihatannya BAGUS tetapi menyimpan Gunung ES yang tinggi dan kita tidak bisa menyelesaikan Problem yang terjadi.
ATAU
RUBAH Pola Pikir kita bahwa Produktifitas kita sebenarnya 71%.... Kelihatan jelek tetapi memang kenyataanya seperti itu dan kita mempunyai RUANG IMPROVEMENT yang lebih luas untuk mencapai 85% bahkan ke angka 90% atau lebih.
Untuk mempelajari TPM lebih detail silahkan berkunjung ke
Atau ingin lebih dalam mempelajari TPM Project, silahkan berkunjung ke
Salam
Indro Agung Hadoko
Cikarang, Medio April 2015
Jumat, 20 Maret 2015
The Power of Stream Mapping & Interaction Between Processes
Saat ini saya sedang mengerjakan project "Productivity Improvement" di salah satu Automotive Parts Company di bilangan Jababeka Cikarang - Bekasi Jawa Barat. Salah satu kawasan area industri yang sangat luas di Jawa Barat.
Langkah awal di dalam project ini adalah mencari dan menentukan Pemborosan-Pemborosan / Waste yang terjadi dalam proses manufacturing. Dengan mengetahui waste yang terjadi maka Kaizen / CI akan lebih mudah dijalankan.
Seperti yang telah kita ketahui bahwa kekuatan Kaizen / CI bukanlah aktivitas Kaizen itu sediri tetapi kekuatannya ada di Cara Menemukan Pemborosan-Pemborosan yang terjadi di dalam proses Manufacturing kita. Semakin kita jeli dalam menemukan Waste yang terjadi semakin tinggi Produktifitas di dalam area kita.
Salah satu TOOLS Improvement yang digunakan dalam mencari Pemborosan yang ada adalah "Stream Mapping & Interaction Between Processes". Dimana fungsi dari Tools ini adalah mencari Kebuntuan-Kebuntuan yang terjadi di dalam aliran suatu proses. Kebuntuan inilah Waste yang terjadi di dalam aliran proses yang harus dihilangkan.
Seperti contoh Mapping dibawah ini yang menunjukkan hubungan dan interaksi antar proses PPIC - Production - Quality (QA).
Dari mapping diatas terlihat bahwa aliran proses diawali dari datangnya PO Customer yang diterima oleh bagian PPIC. Selanjutnya PPIC akan membuat Schedule to Customer yang akan di informasikan ke Customer.
PPIC juga akan membuat Kebutuhan Raw Material yang ditujukan kepada Purchasing yang selanjutnya akan menunggu datangnya Raw Material yang akan dilakukan pengecekan oleh bagian IQC (Incoming Quality Control).
...... Sampai sejauh ini proses masih mengalir dengan normal.
Selanjutnya PPIC membuat "Planning Produksi" yang diserahkan kepada Production Department (Foreman). Dilain pihak, dengan tujuan untuk memberikan informasi ke Produksi, PPIC juga membuat "Delivery Schedule" yang juga diserahkan kepada Production Department (Foreman).
Di bagian internal Produksi, Production Manager juga membuat Planning Produksi yang diberikan kepada Production Foreman, karena baginya memberikan tugas pekerjaan adalah tugas Production Manager.
Di bagian Delivery, yang merupakan ujung tombak pengiriman dan berinteraksi langsung dengan Customer, juga seringkali memberikan "Planning Produksi" menurut versi mereka kepada Production (Foreman).
........ Disinilah awal kekacacaun proses itu terjadi.
Bisa dilihat di Mapping, terlihat Production (Foreman) menerima 4 (empat) Production Planning dari 4 arah. Apa akibatnya? Production Foreman akan mengalami kesulitan Production Planning mana yang akan dijadikan referensi. Semua arah merasa Penting dan paling benar akan Production Planning yang mereka buat.
Proses ini terus menerus terjadi.... Setiap Hari..... Mengalir ... dengan segala Kekacauan Aliran yang terjadi..... tanpa pembenahan sama sekali.
Akibat dari itu semua adalah: LOW PRODUCTIVITY & QUALITY.
Dengan menggunakan TOOLS "STREAM MAPPING & INTERACTION BETWEEN PROCESSES".... akan tertangkap segala macam SUMBATAN yang terjadi di Aliran Proses serta Pemborosan-Pemborosan lainnya.
Langkah selanjutnya adalah menentukan Langkah KAIZEN / CI yang tepat untuk Problem diatas yang tentunya akan lebih mudah menentukannya.